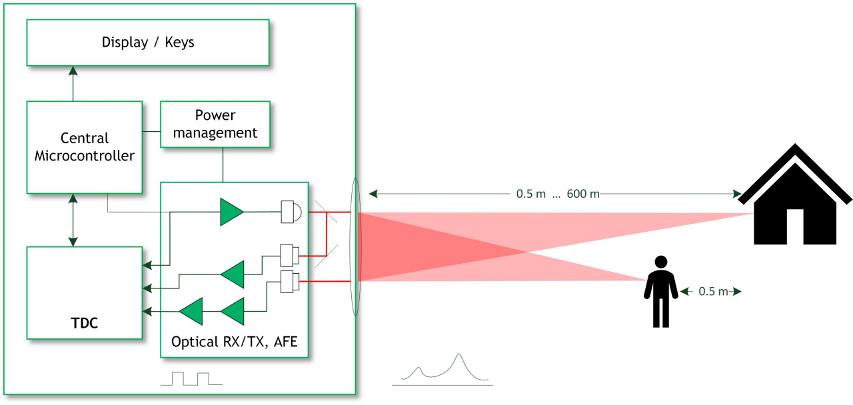
LTDC-X3, as it will be known, offers single-shot resolution of up to 20ps(rms).
The chip has one ‘start’ input and two ‘stop’ inputs, and calculates the time differences between the start channel and the stop channels.
“In typical lidar designs, the start will be triggered by the laser trigger, stop1 by the reference beam, and stop2 will be the main measurement channel,” according to the company. “On both channels the chip measures rising and falling edge and therefore the time-of-flight and the pulse width for each hit.”
Stop measurement of up to four pulses is possible, resolution is typically 30ps(rms) and maximum measuring time is 2.4us – with time measurements continuously calibrated against a reference clock from a 4 – 20MHz crystals.
“By taking advantage of the combination of high precision and multiple stop triggers, a lidar can generate a detailed and accurate picture of the complex environment through which a drone or robot might navigate,” according to ScioSense.
Read our full Electronica 2024 coverage »
Connection to the external analogue front-end if via LVDS inputs, and communication with a host processor is via a 50MHz quad SPI interface that can transfer data at 200Mbit/s.
Operation is from 3.3V over -40 to +125°C, and power dissipation from the 4 x 4mm QFN package is and 150mW.
“Many industrial lidar systems continue to rely on an FPGA to provide the interface to a laser diode emitter and detector,” asserted ScioSense marketing director Norbert Breyer. LTDC-X3 gives lidar manufacturers a smaller option which consumes less power.”
Aside from robots and drones, applications are foreseen in golf range finders and safety scanners.
ScioSense is headquartered in Eindhoven.
Find out about the time-to-digital IC on stand B3.419 at Electronica in Munich this week, or on this LTDC-X3 data sheet.